MIM Parts
MIM Parts
Blog Article
Metal Injection Molding (MIM) parts are precision-engineered components created through an advanced manufacturing process. These MIM parts excel in producing intricate designs with high accuracy. Industries increasingly adopt MIM technology due to its efficiency. For instance, the global MIM parts market, valued at $1.5 billion in 2022, is projected to reach $3.1 billion by 2030.
Key Takeaways
- MIM parts are strong like metal and shaped with molds. They are great for tricky uses in cars and medical tools.
- The MIM method saves money and works fast. It makes many detailed parts with little wasted material.
- Picking the right material for MIM parts is important. It affects how well they work, last, and cost in different uses.
What Are MIM Parts?
Definition and Characteristics
MIM parts are components manufactured using the Metal Injection Molding process, a technique that combines the versatility of plastic injection molding with the strength of metal. These parts are known for their ability to achieve intricate geometries and high precision, making them suitable for complex applications. MIM parts typically exhibit densities ranging from 95% to 99% of wrought metals, ensuring excellent mechanical properties. They also maintain tight dimensional tolerances, often within ±0.1%, which is critical for industries requiring high accuracy.
The characteristics of MIM parts extend beyond precision. They offer high corrosion resistance, mechanical strength, and durability. These properties make them ideal for sectors such as automotive, aerospace, and medical devices. For example, automotive applications include gears and rocker arms, while medical uses range from surgical instruments to implants. The ability to produce lightweight yet robust components further enhances their appeal across industries.
Why MIM Parts Are Important
MIM parts play a vital role in modern manufacturing due to their cost-effectiveness and versatility. The process allows for mass production of complex components at a lower cost compared to traditional methods like CNC machining or casting. This efficiency is particularly beneficial for industries such as healthcare, where demand for small, intricate parts continues to grow.
The material flexibility of MIM parts also contributes to their importance. Manufacturers can choose from a wide range of metals, tailoring the material properties to specific applications. For instance, aerospace components like turbine blades and nozzles benefit from the high strength and lightweight nature of MIM parts. Additionally, the precision of these parts ensures consistent performance, reducing the need for secondary machining or adjustments.
Tip: MIM parts are a preferred choice for industries aiming to balance performance, cost, and design complexity.
How Are MIM Parts Made?
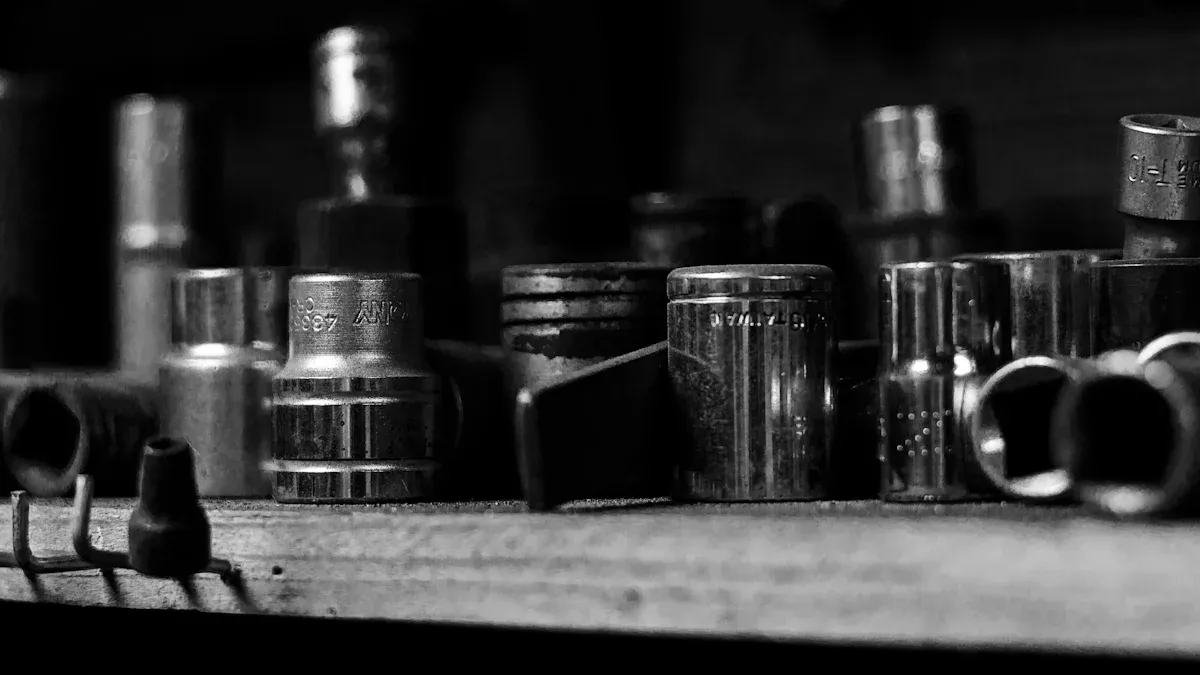
Overview of the MIM Process
The Metal Injection Molding (MIM) process combines the precision of injection molding with the strength of metalworking. It is a multi-step manufacturing technique designed to produce high-quality, intricate components. This process begins with the creation of a feedstock by blending fine metal powders with a thermoplastic binder. The feedstock is then injected into a mold to form the desired shape, known as the "green part." Subsequent steps remove the binder and densify the metal, resulting in a finished product with excellent mechanical properties.
MIM technology is particularly advantageous for producing small, complex parts with tight tolerances. The process achieves dimensional precision down to ±0.1% and surface finishes as fine as 0.5 μm Ra. These capabilities make it a preferred choice for industries requiring high-performance components, such as medical devices and aerospace.
Key Steps in Manufacturing
The MIM process involves several critical stages, each contributing to the final product's quality. The table below outlines these steps:
Stage | Description |
---|---|
Feedstock Preparation | Fine metal powders are blended with a thermoplastic binder to create a homogeneous feedstock. |
Injection | The feedstock is heated and injected into a mold, forming the "green part." |
Debinding | The binder is removed using thermal or solvent-based methods, leaving a porous "brown part." |
Sintering | The brown part is heated to bond the metal particles, achieving final dimensions and properties. |
Post-Processing | Optional processes like machining or heat treatment refine the part to meet specific requirements. |
Each stage plays a vital role in ensuring the final product meets stringent industry standards. For example, sintering densifies the metal, enhancing its strength and durability. Post-processing further tailors the part to specific applications, such as improving surface finish or achieving tighter tolerances.
Note: The efficiency of the MIM process allows manufacturers to produce MIM parts with minimal material waste, making it both cost-effective and environmentally friendly.
Materials Used in MIM Parts
Commonly Used Materials
The materials used in MIM parts must meet stringent requirements to ensure optimal performance. Ideal materials exhibit excellent flowability, high strength, and good dimensional stability. They also require favorable sintering characteristics, such as low shrinkage and minimal distortion. Commonly used materials include stainless steels, low-alloy steels, tool steels, titanium alloys, and nickel-based superalloys.
Material Type | Common Grades | Applications | Key Properties |
---|---|---|---|
Stainless Steel | 17-4PH, 316L, 420 | Aerospace, automotive, medical, food production | Strength, corrosion resistance, affordability |
Low Alloy Steel | 4140, 2200 | Automotive, aerospace, defense | Toughness, strength, hardenable |
Tool Steel | HSS, HWS | Metalworking, plastics processing, electronics | Hardness, wear resistance, thermal stability |
Titanium Alloys | Ti-6Al-4V, Ti-6Al-7Nb | Aerospace, medical | High strength-to-weight ratio, corrosion resistance |
Nickel-Based Superalloys | Inconel, Hastelloy | Aerospace, energy | Exceptional mechanical properties, thermal stability |
The global MIM market, valued at $1.5 billion in 2022, is projected to grow at a CAGR of 8.7%, reaching $3.1 billion by 2030. This growth reflects increasing demand for larger and more complex MIM components across industries like healthcare, automotive, and aerospace.
Material Selection for Applications
Selecting the right material for MIM parts depends on application-specific requirements. Factors such as sintering temperatures, cost, mechanical properties, and secondary processing needs play a critical role. For instance, stainless steel 316L is ideal for surgical instruments due to its corrosion resistance, while titanium Ti-6Al-4V is preferred for aerospace and medical implants because of its high strength-to-weight ratio.
Material | Applications |
---|---|
Stainless steel 316L | Surgical instruments, pumps, valves |
Tool steel H13 | Injection molding, extrusion, dies |
Titanium Ti-6Al-4V | Aerospace, medical implants |
Tungsten heavy alloys | Radiation shielding, vibration damping |
Copper alloys | Electrical contacts, thermal management |
Ceramics | Cutting tools, wear parts, ballistics |
Comprehensive quality control ensures defect-free components that meet application demands. The chart below highlights the frequency of materials used across various applications:
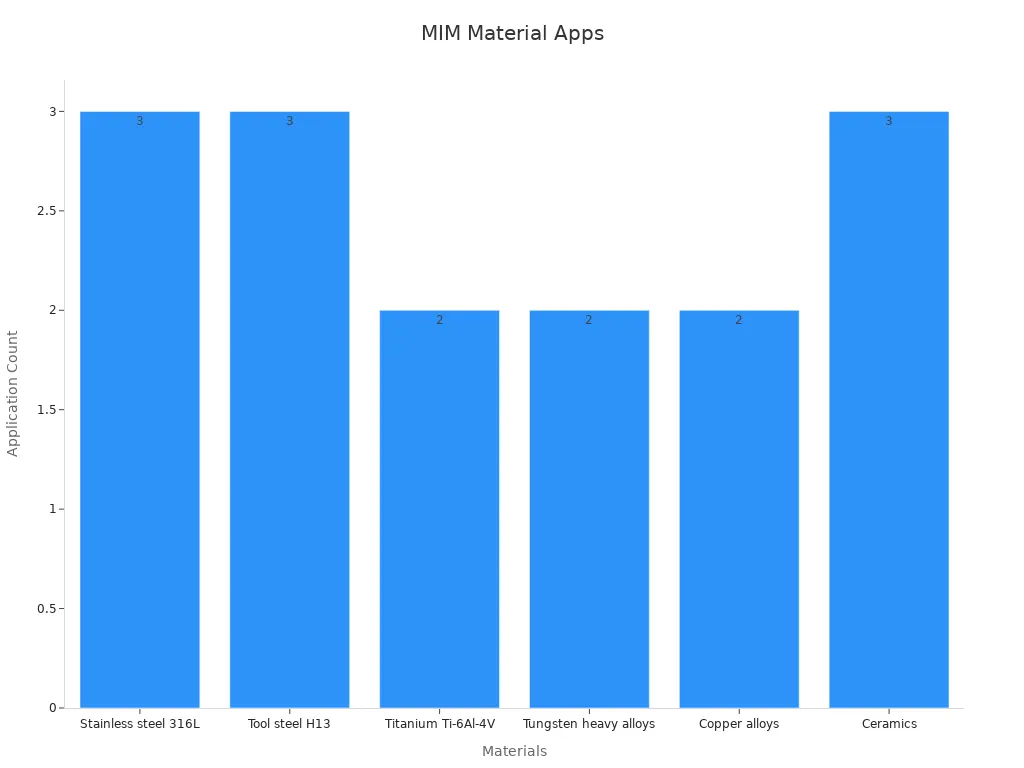
Note: Material selection directly impacts the performance, durability, and cost-effectiveness of MIM parts.
Applications of MIM Parts
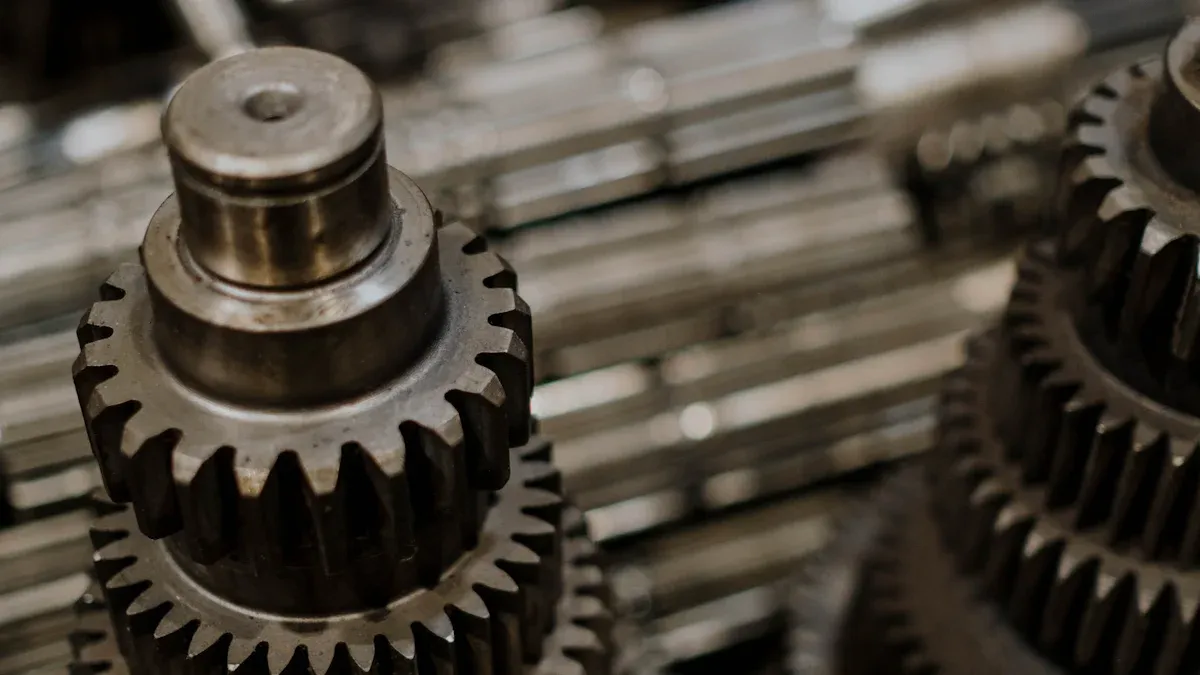
Medical and Surgical Tools
MIM parts are revolutionizing the medical industry by enabling the production of high-precision components for surgical tools and implants. The process allows manufacturers to create intricate designs that meet the stringent requirements of medical applications. For example, stainless steel 316L is commonly used in surgical instruments due to its corrosion resistance and biocompatibility. Titanium alloys, such as Ti-6Al-4V, are preferred for implants because of their lightweight and durable properties.
The medical devices segment is experiencing significant growth, driven by the increasing demand for minimally invasive surgical tools and advanced implants. MIM technology ensures consistent quality and performance, reducing the need for secondary machining. This makes it an ideal choice for producing components like forceps, scissors, and dental implants. The versatility of MIM parts highlights their importance in advancing healthcare solutions.
Automotive and Aerospace Components
The automotive and aerospace industries rely heavily on MIM parts for their ability to produce lightweight, durable, and complex components. MIM technology is particularly effective for creating small, high-precision parts that meet strict performance standards. For instance, automotive manufacturers use MIM parts for gears, rocker arms, and fuel injector components. In aerospace, turbine blades and nozzles benefit from the process's ability to combine strength with intricate designs.
- MIM offers cost advantages over traditional methods like machining and casting, especially for medium to high production volumes.
- The process enables the production of multi-component designs in a single part, reducing assembly time and costs.
- Lightweight and durable components produced through MIM are essential for electric vehicles and high-performance aerospace applications.
The growing demand for electric and hybrid vehicles further emphasizes the importance of MIM technology in these sectors.
Electronics and Consumer Products
The consumer electronics sector is a major driver of the MIM market, with applications in devices like smartphones, laptops, and wearables. MIM parts are ideal for producing intricate and miniature components, such as connectors, hinges, and camera housings. The process ensures high precision and consistent quality, meeting the demands of modern electronics.
Segment | Insights |
---|---|
Consumer Electronics | Expected to hold the largest market share in 2025 due to rising demand for MIM parts in smartphones and laptops. |
Medical Devices | Anticipated significant growth driven by demand for MIM parts in surgical instruments and implants. |
Geographical Insights | Asia Pacific is projected to be the largest market, with China as a major contributor. |
The rapid growth of the consumer electronics sector underscores the importance of MIM technology. Additionally, the process is widely adopted in the firearms industry for components like trigger guards and bolt sleeves, simplifying production and reducing costs. The versatility of MIM parts ensures their continued relevance across diverse applications.
Advantages of MIM Parts
Cost and Material Efficiency
MIM parts offer significant cost and material efficiency, making them a preferred choice for industries requiring high-volume production. The process minimizes material waste by producing near-net-shape components, reducing the need for extensive post-processing. This efficiency translates to lower material costs and shorter production times.
Advantage | Description |
---|---|
Cost-effectiveness at scale | MIM can be more economical than machining, casting, or stamping for large-scale production. |
Reduced waste | The near-net-shape capability minimizes material loss during manufacturing. |
MIM technology also supports the use of advanced metal alloys, enabling manufacturers to achieve superior mechanical properties without excessive costs. For example, automotive manufacturers benefit from the ability to produce durable, lightweight components at a fraction of the cost of traditional methods.
Note: MIM parts combine cost savings with material efficiency, making them ideal for industries like automotive and aerospace.
Precision and Design Complexity
The precision and design flexibility of MIM parts set them apart from other manufacturing methods. The process achieves dimensional tolerances as tight as ±0.1%, ensuring consistent quality across production runs. Fine details, such as surface finishes down to 0.5 μm Ra, are also possible.
- MIM enables the creation of intricate geometries that are difficult to achieve with traditional methods.
- Most parts are sintered to their final dimensions, reducing the need for secondary machining.
This capability allows manufacturers to produce complex components with excellent mechanical properties. For instance, MIM combines the design flexibility of plastic injection molding with the strength of machined metal parts, making it suitable for advanced applications in medical devices and aerospace.
Scalability for Mass Production
MIM technology excels in scalability, making it an attractive option for mass production. The global production of MIM parts exceeds 200 million units annually, highlighting its capacity to meet high-volume demands. Initial tooling costs are offset by lower costs per unit as production volumes increase.
- MIM supports the production of large quantities of high-precision components.
- The process is cost-effective for mass production, especially for industries like consumer electronics and automotive.
This scalability ensures that manufacturers can meet growing market demands without compromising quality or efficiency. The ability to produce consistent, high-quality parts in large volumes underscores the value of MIM technology in modern manufacturing.
MIM Parts vs. Other Manufacturing Methods
Comparison with CNC Machining
Metal Injection Molding (MIM) and CNC machining are both widely used manufacturing methods, but they cater to different needs. MIM excels in producing small, intricate parts at high volumes, while CNC machining is better suited for low-volume production or parts requiring extensive customization.
Key differences between the two methods include production speed, material wastage, and precision. The table below highlights these distinctions:
Aspect | MIM | CNC Machining |
---|---|---|
Production Speed | More efficient for high volumes | Fast but limited by setup time |
Design Complexity | Handles complex geometries | Can produce detailed parts but less complex than MIM |
Material Wastage | Lower wastage | Higher due to cutting process |
Precision | Higher precision | Good precision but affected by tool wear |
MIM offers significant advantages for mass production. It minimizes material waste and reduces the need for secondary machining. CNC machining, on the other hand, provides flexibility for prototyping or low-volume runs but generates more waste due to its subtractive nature.
Comparison with Casting
Casting and MIM share similarities in producing metal components, yet their applications differ. MIM is ideal for creating high-precision parts with complex geometries, while casting is better suited for larger components or simpler designs.
Key advantages of MIM over casting include:
- Cost-effectiveness for small, intricate parts.
- High accuracy and consistency in production.
- Reduced need for secondary machining operations.
Casting often struggles with achieving the same level of precision as MIM. Additionally, MIM parts exhibit superior mechanical properties due to their higher density and tighter tolerances. These factors make MIM a preferred choice for industries requiring high-performance components.
Tip: Manufacturers should evaluate production volume, design complexity, and material requirements when choosing between MIM and alternative methods.
MIM parts represent a breakthrough in modern manufacturing, combining precision, efficiency, and versatility. Their production process ensures high-quality components with minimal waste. Industries benefit from their adaptability to various materials and applications. The table below highlights their key advantages:
Advantage | Description |
---|---|
Cost Advantage | MIM provides a cost advantage over machining and casting for medium to high production volumes provided secondary processing is minimal. |
Economic Benefits | The process offers the highest economic benefits for complex, multi-component designs consolidated into a single MIM part. |
These attributes make MIM parts an indispensable solution for industries seeking innovation and cost-effectiveness.
FAQ
What industries benefit the most from MIM parts?
Industries like medical, automotive, aerospace, and electronics benefit significantly. MIM parts provide precision, cost-efficiency, and material versatility, making them ideal for high-performance applications.
How does MIM compare to traditional manufacturing methods?
MIM excels in producing intricate, high-volume parts with minimal waste. It outperforms traditional methods like casting and machining in cost-effectiveness and design complexity.
Can MIM parts replace machined components?
Yes, MIM parts can replace machined components in many cases. They offer comparable strength and precision while reducing production costs for complex, high-volume designs.
Tip: Evaluate application requirements to determine if MIM is the optimal choice for replacing traditional components.Report this page